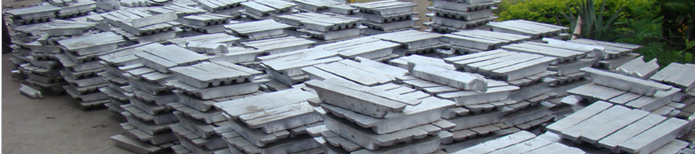 |
|
 |
Home »
Our Product » Battery Recycling
Battery Recycling
The battery-recycling has changed dramatically over
the past ten to twenty years. The changes have resulted from environmental
regulation, changes in battery-processing technology, changes in battery
distribution and sales techniques, changes in lead-smelting technology, and
changes in the lead alloys used in the batteries.
Battery Scrap Collection And Processing
In the 1970s, batteries were distributed primarily
through full-service gasoline stations. Smaller amounts were distributed
through hardware stores, automobile supply stores, and mass merchandise
outlets. The scrap batteries were recovered by the service stations and sold
to scrap dealers, who also recovered batteries from wrecked or worn-out
automobiles. The scrap dealers then sold the batteries to battery breakers
and smelters. The higher lead content of the battery plates made it
cost-effective to ship plates longer distances than whole batteries.
Environmental Regulations
In the 1980s, environmental legislation was passed
regulating lead acid battery recycling. Rules were promulgated regarding the
storage, processing, and transportation of batteries and battery scrap.
Batteries and battery components are considered hazardous waste after
arrival at a battery breaker or smelter if they are cracked or leaking acid,
or if they are disposed of in landfills. Scrap batteries can be stored for
only 90 days, after which they must be sent to a recycler or disposed of in
a hazardous-waste landfill. Because only permitted processors can break
batteries, the number of battery breakers has declined markedly. Only a few
breakers still remain. Battery breaking is now performed mainly by lead
smelters.
Battery-Breaking Processes
In the 1970s, most battery breakers used saws for
decasing. In this process, the top is severed, the acid is drained, and the
plates are dumped from the case. The lead posts are recovered from the tops
by crushing and separation. This process is still utilized by many lead
smellers in the United States and throughout the world.
In the late 1970s and early 1980s, several mechanical processes were
developed to break the batteries. Technologies were developed to crush the
whole batteries, separate the case from the lead-bearing materials, separate
the hard rubber (ebonite) and separators from the plastic cases, and, in
some cases, separate the paste portion of the battery from the metallic. The
acid is neutralized in a separate procedure.
A recent innovation desulfurizes the paste, produces lead carbonate,
recovers sodium sulfate crystals, and recycles the H2O. Virtually all
battery-wrecking processes now recycle the polypropylene battery cases.
Battery breakers process from 5000 to more than 50000 spent automobile
batteries per day.
Lead Smelting Processes
The major smelting processes to recycle lead scrap
involve the use of blast furnaces, short rotary furnaces, long rotary kilns,
reverberatory furnaces, electric furnaces, and top-blown rotary furnaces.
Rotary Furnaces
In most of the world other than the U.S., rotary
furnaces (long, short, and top blown) have replaced blast furnaces as the
major smelting vessels for lead recycling. Rotary furnaces are very
versatile. They can accept virtually any type of lead-bearing feed material,
including battery scrap, dust, dross, scrap lead, and sludge. Rotary
furnaces can use any carbon source such as coal, coke, or ebonite as
reducing agent, and they can use a variety of fuels, such as oil, coal, or
gas. Because they are batch furnaces, rotary furnaces can be operated in
stages to produce low-impurity bullion for refining to pure lead, or they
can completely reduce the charge to recover all metal values for production
of lead-antimony alloys. Rotary furnaces generally use Na2CO3 and iron as
fluxes, which produce a fluid, low-melting slag.
Scrap As Charge For Primary Lead Furnaces
Recycled battery scrap, particularly the paste
portion, is often added in small amounts to the charge of sinter machines in
primary-lead smelters. New lead-smelting processes can utilize lead battery
paste as a substantial portion of the charge.
Lead Blast Furnaces
Small amounts of lead are recycled via lead blast
furnaces. The primary materials recycled in such furnaces are lead-coaled
power and communications cable, lead sheet and pipe, and other products that
contain lead as a coating or as part of a complex part. The process is
performed at relatively low temperatures and produces both metal for
refining and dross; the dross is recycled to smelters.
Specifications For Recycled Lead
Throughout much of the world, two lead
specifications prevail: one with a minimum of 99.99% Pb and the other with a
minimum of 99.97% Pb. The major impurities in lead are antimony, arsenic,
bismuth, copper, nickel, silver, tin, and zinc. Recently, selenium and
tellurium have been added as important impurities.
Primary-lead companies generally produce the 99.99% Pb grade, whereas
recyclers produce the 99.97% Pb grade. The major difference in the lead
grades is that recyclers generally do not remove the bismuth and silver in
their refining process. Recycled lead generally contains sufficient bismuth
to preclude reaching 99.99% purity.
Gas-Producing Impurities
More important than restrictions of bismuth and
silver in lead specifications has been the restriction of elements that
increase gas generation in lead acid batteries. Elements that promote
decomposition of the electrolyte and production of gas upon charging are
specified at very low levels regardless of the overall purity of the lead.
The specification for pure lead for battery oxide restricts antimony,
arsenic, nickel, and tellurium to low levels, whereas non gassing impurities
such as bismuth, silver, and copper are permitted at higher levels. In the
most restrictive specifications, all the gas-producing impurities are
restricted to a content of 1 ppm or less.
Government Regulations Regarding Recycling
The lead industry, and particularly the lead
recycling industry, must conform to increasingly stringent environmental
regulations. Lead acid batteries, the major raw material of recyclers, have
been declared a hazardous waste. Because batteries are the largest source of
lead, they constitute the major source of lead contamination in landfills
and incinerators.