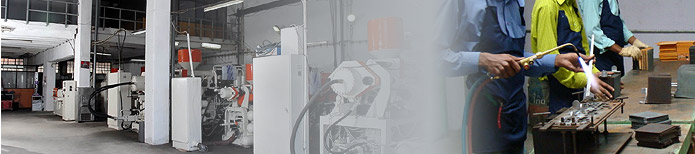 |
|
 |
Home »
Our Product » Acid Draining Machine
Acid Draining Machine
Batteries are loaded on battery feed conveyors and
it passes through Acid Extraction/ Draining machine that is mounted on FEED
CONVEYORS. Acid is automatically drained out from battery & acid is sent
to its storage tank. Acid stored in a tank, the precipitated oxide slurry is
taken out with the valve & the acid is sending for Recycling.
(Conveyorised)
Once Battery is cut and now only Plates with
separator are there in Plastic container. There may be acid in the Battery
Container still. Battery will drop in upside position, manually assisted.
Container can be picked up and placed at a side or drop in Plastic Crusher.
Battery Plates and Separator can be Transported to Plate Crushing Machine.
Acid will drop in tank. Acid Proof Tank is in-built in the attachment. Lead
Oxide Dust and small grid parts will precipitate. Acid can be pumped out, if
connected to another tank. Lead Sludge can be charged in furnace.
Acid Collection & Filtration Unit
Acid stored in a tank, the precipitated oxide slurry
is taken out with the valve & the acid is sending for Recycling:
Neutralization. It can be handled in two ways: First way, the acid is
neutralized with an industrial compound similar to household baking soda.
Neutralization turns the acid into water. The water is then treated;
cleaned, tested in a waste water treatment plant to be sure it meets clean
water standards. Second way, the acid is processed and converted to sodium
sulfate, an odorless white powder that's used in laundry detergent, glass,
and textile manufacturing.
Battery Cutting System
Conveyor can be connected to the Lorry which
carrying the Scrap Batteries to have lesser manual shifting of batteries. It
is an additional requirement which is chargeable at additional costs. It is
integral unloading and feeder to Lid Shaver Machine. We shave the Battery
from under its cell straps. Proper Cooling Arrangements are made, that
enhances the machine's life so the cutting equipment gets cool at the time
of cutting battery's lid parts. Now, the shaved lid which is separated from
under the welded straps is sent through conveyor to Lid Crusher Machine.
Parts Separation Machine
The Lid part is completely crushed and sent to
Lead-Plastic separating Machine: i.e., Metal Classifier; with this process
plastic parts are separated from the Lead parts. Such plastic parts are sent
to the Plastic Crusher & are cut into smaller pieces. The Rest
of the battery is moved on conveyor to the PART SEPARATOR MACHINE &
all the parts are separated totally and sent to their separate respective
storage tanks with the help of Conveyor systems. This separation machine is
enclosed & no dust particles come out of the plant this increases plants
recovery & reduces wastages of material. For dust collection BAG HOUSE
is attached so that the oxide dust is stored in a filter bag. In this
machine, on the First stage, the Battery Casings are taken out & sent to
their separate section through its connecting conveyor. Later on, these
Casings are sent to the same earlier Plastic Crusher, or a separate crusher
can be placed as per customer's choice at additional cost which depends upon
the Production capacity of the plant.
After this step, the Plates & Separators are sent to the second level,
in this section using a particular stage of vibration resonance at certain
level we have taken out maximum quantity of Lead parts from the Plates &
Shredded oxide material on the Third stage for Collection in its particular
storage tank. In this stage, we took out the impregnated material from the
plates on Grid. The rest material on plates are taken out with Battery
Separators are sent to the Part Separation Machine on which the Plates are
separated on one stage i.e., on one side & Separators are stored on
other side. The Plate Parts & Separator Parts are separated and here we
are collecting the rest of the shredded oxide material. The Grid parts &
separators are separated by using the Grid-Separator Separation Machine. In
this machine, Both Grids parts & separator parts are dropped through
conveyor. Heavy air & water pressure is given simultaneously in the
machine and by using floatation method we are separating the Separators &
Grid Parts. These shredded Plates are sent to the FURNACE FOR SMELTING
[Recycling]. And the Separators are sent through conveyors to A Separator
Washing Machine. This separator washing machine is added to the system as
per the customer's on demand or as per the plant production capacity. The
machine is completely enclosed and environment friendly. Getting back on
Parts Separation Machine, in the third layer of separation, Broken Separator
Parts, Broken Grid Parts & Oxide Dust is taken out & sent to the
other Metal Classifier & Floatation Tank is attached on that. In this
section, Separator parts floats in water tank. The Lead Parts & the
Oxide dust is settled down on the bottom side of the tank due to its weight
& taken out with the help of rotary valve. And, the same water can be
used again & again. The transferring of Lead Parts & Oxide Dust
material can be sent to their respective Refining Pots & Smelting Units
through Fork Lifts/ automatically with the help of automated mechanized
system that will be on customer's demand at additional cost.
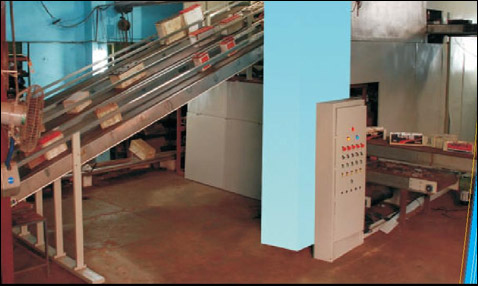
Plastic Crushing Machine
The shaved lid which is separated from under the
welded straps is sent through conveyor to Lid Crusher Machine. Plastic parts
are separated from the Lead parts. Such plastic parts are sent to the
Plastic Crusher & are cut into smaller pieces. This machine is used to
crush Battery Container made of Plastic Material. It crushes to small Pieces
up to size of 1" square in one go and Washes Lead accumulated on it. It
is shearing & hammering action increases its Power versus Output Ratio.
Lead is precipitate on another conveyor. This conveyor conveys Lead
Particles/ Pieces to one side. Plastic which can float on water will be
filtered on another Conveyor. Plastic is fed to Plastic Washing Machine.
This Plastic Washing Machine washes Plastic with Soap Solution. Plastic is
filtered and collected. Water is used again after purification.
- Total Power: 56 H.P./42Kw.
- Container Feeding Conveyor: This conveyor is used for feeding Plastic
- Container to Plastic Crusher: M.S. material makes. The Drive of
Electrical, 415V/380V, 3 Phases, 50Hz, 0.5 HP
- Crushed Plastic Feeding Conveyor: This conveyor is used for feeding
crushed plastic to Plastic/ Lead Separation Machine; It is of MS
material.
Plastic Washing Machine
The crushed plastic is sent to Plastic Washing
Machine through Feed Screw Conveyors to Floating Washing Machine. The
plastic is washed & lead Contents sinks to the bottom of machine, the
plastic is simultaneously forwarded ahead to the hot washing machine. Then
the plastic is taken out with the help of Screw Conveyor from other end &
put up in centrifugal de-watering machine, the washed plastic is taken out
with the blowing system through Blower. The washed clean plastic is then
stored in a storage bunker from there the material can be stored in bins or
sacks. The machines are included in system are:
- Feeding Screw Conveyors
- Floating Washing Machine
- Hot washing Machine
- De Watering Machine
- Air Blown Pipeline
- Blower Fan
- Storage Bunker
[The size of the machines are designed according to their
production capacity]
Separator Washing Machine & Lead Paste Filtration Unit
A Separator Washing Machine; This separator
washing machine is added to the system as per the customer's on demand or as
per the plant production capacity. The machine is completely enclosed and
environment friendly. The separators are fed to the machine through Screw
Conveyor from one side & washed in the machine & are taken out from
other end. The lead contents sinks & taken out with the help of rotary
valve & stored in a storage pit. The Lead paste is then filtered &
De-suphurized with the Desulphurisation Unit.